Evitez le reengineering, adoptez le Lean Management !
- lfarcinade
- 28 sept. 2020
- 8 min de lecture
Dernière mise à jour : 22 juin
Par Sylvain DEMURE, Consultant Cost House France
Alors que les méthodes de reengineering s’inscrivent dans des solutions de rupture et sont relativement directives, l’approche dite « Lean Management » relève d’une démarche d’amélioration continue et progressive, en y intégrant un maximum d’acteurs.
Le Lean Management, nouveau levier de compétitivité
Dès les années 80, le Lean Management s’est imposé comme méthode de productivité à l’instar du Taylorisme ou du Fordisme en leurs temps, ou encore du Toyotisme dont il découle.
Il se définit comme une logique d’organisation et un système de management destinés à créer de la valeur pour les clients, à supprimer les tâches sans valeur ajoutée et les gaspillages afin de focaliser les ressources sur l’essentiel.
Le Lean Management repose donc sur la mise en place et l’adoption dans l’entreprise de:
La généralisation des principes du toyotisme à toutes les fonctions et les secteurs d’activité
La limitation des « gaspillages »
La recherche de multiples outils et méthodologies d’optimisation du temps de production
Respect de l’intelligence du salarié
Simplification de la hiérarchie
Bien qu’il ne lui soit pas réservé, c’est dans l’industrie que l’apport du Lean Management en termes de compétitivité fut le plus flagrant. En s’opposant ainsi au système de production de masse privilégié par General Motors aux US, et à la suite de l’étude du MIT en 1986 (voir tableau ci-dessous), l’usine Toyota de Takaoka au Japon prouva l’efficacité de la méthode (temps de stockage et d’assemblage, défauts de conception, etc).

Transformer sa façon de penser pour réussir sa transition vers le Lean Management
Il est essentiel de rappeler que la mise en place d’une démarche de Lean Management se base sur un processus d’amélioration continue. Elle contraste en cela avec les approches de reengineering qui s’inscrivent dans des solutions de rupture.
L’esprit de la méthode Lean Management et ses valeurs peuvent se résumer ainsi :
C’est une approche fondamentalement orientée vers la satisfaction client, par la qualité du produit ou du service
Le management doit être à l’écoute des équipes qui rencontrent des difficultés sur le terrain
Les solutions doivent être coconstruites avec les équipes et non imposées par des experts ou par le management
Les outils doivent rester simples et s’appuyer sur le bon sens
On ne cherche pas à faire une révolution mais à améliorer petit à petit, par petits pas, la performance collective
A l’opposé de l’approche Taylorienne qui place les processus, les règles et les outils au premier plan, l’approche Lean s’appuie sur la conscience individuelle et collective de la qualité et de la valeur ajoutée pour le client
Plus encore que les équipes, le management doit donc être accompagné pour changer son positionnement et son fonctionnement :
Le responsable n’est pas là pour donner des ordres mais pour écouter et aider
Le responsable n’est pas là pour avoir la solution, mais pour permettre à son équipe de trouver les solutions
L’information n’est pas réservée au management mais doit être partagée
Focus sur la limitation des gaspillages et l’optimisation du temps de production :
Comme mentionné précédemment, l’un des objectifs du Lean Management vise à éliminer les gaspillages ou MUDA en japonais, c’est-à-dire les activités qui n’apportent pas de valeur ajoutée (gaspillages, pertes, dysfonctionnements, etc.).
Les 7 principaux gaspillages peuvent se résumer ainsi :
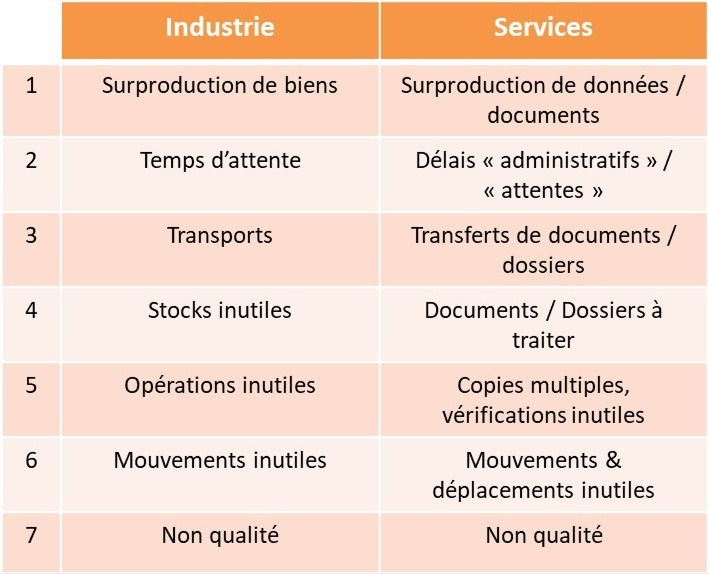
À ces sept gaspillages originels s’est ajouté un huitième qui correspond à la mauvaise gestion du temps et la sous-utilisation des compétences (manque d’implication et de participation de tous les membres de l’équipe) :
Refaire ce qui a été déjà réalisé une première fois
Assumer une tâche qui devrait être accomplie par une autre fonction
Faire à la place de ses collaborateurs (j’irai plus vite, ils n’ont pas le temps…)
Le Lean Management tend également à améliorer le niveau de production, partant du principe qu’un processus est efficace quand :
Il est juste-à-temps (la valeur au plus tard, au juste nécessaire)
Il permet de produire bon à chaque étape
Le « Just in Time » ou juste à temps va permettre de ne produire que ce que le client achète ou a déjà acheté dans le cas d’une production à la commande. Pour atteindre cet objectif, l’ensemble des flux de l’usine, ainsi que ceux en amont (fournisseurs) et ceux en aval (distribution) sont organisés en appliquant les principes et outils suivants :
Flux tiré (la production est synchronisée avec le besoin du client)
Takt time (c'est l'unité de temps qu'il faut pour livrer au client 1 pièce)
Kanban (La fabrication est pilotée à l’aide d’un système visuel)
Mise en pratique de la méthode et présentation des outils :
Afin de garantir la bonne mise en œuvre et la réussite de la méthode, le Lean Management doit reposer sur les principes suivants :
S’assurer que les objectifs viennent du client
Mener la chasse au gaspillage
Connaître le terrain
Adopter une approche collaborative
Mesurer sa performance
Préférer le progrès continu à la rupture
Mettre en place un management visuel
Stabiliser – Standardiser
S’engager dans la durée
Chaque manager doit impérativement assimiler le Lean à une méthode de management s’il veut en faire le meilleur usage et éviter une utilisation dévoyée de sa finalité, risquant d’aboutir ainsi à une perception négative.
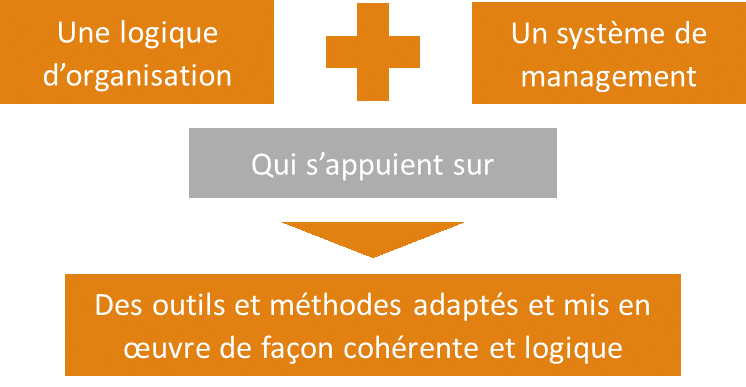
Ainsi, mettre en œuvre les outils du Lean c’est réfléchir aux conséquences et impacts d’un fonctionnement verticalisé pour mettre en place un fonctionnement transverse :
Donner de la visibilité à l’ensemble des acteurs du processus
Supprimer les gaspillages et les opérations inutiles
Rendre le processus plus fluide, agile et réactif
Équilibrer les charges aux postes de travail
Améliorer la conformité des produits
Supprimer les goulots d’étranglement
Améliorer les conditions de travail
etc
Les principaux outils du Lean peuvent être regroupés par thème et par champs d’actions comme suit :
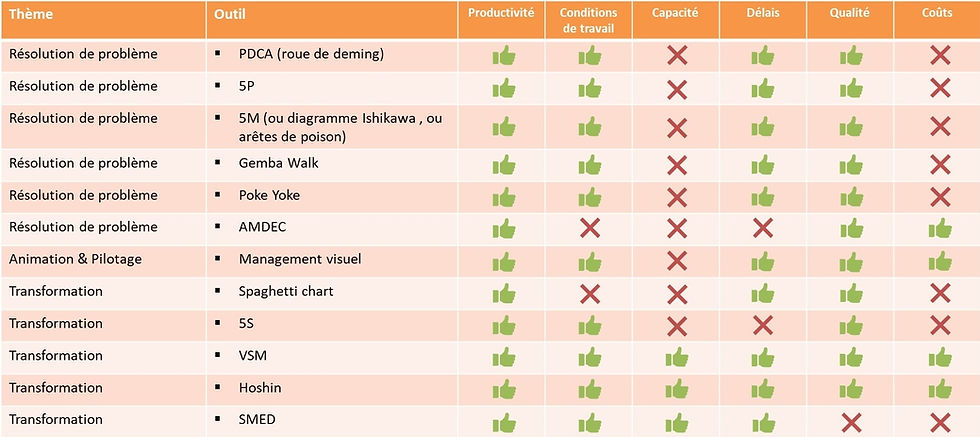
PDCA
Le cycle PCDA a été conçu dans le but d’établir un modèle continu pour l’amélioration constante des processus : une gestion de la qualité efficace et continue. Cependant, le modèle peut être utilisé dans de nombreux contextes, en particulier par le biais des extensions de Deming. Derrière le cycle PDCA se cache un modèle utile pour tout processus d’apprentissage et d’amélioration.
Pour cela, il faut suivre les étapes Plan-Do-Check-Act, que l’on peut traduire en français par : planifier, développer, contrôler, agir. Cela peut s’appliquer aussi bien aux processus de travail qu’aux produits et services qui en découlent, mais aussi aux personnes elles-mêmes. Le cycle PDCA permet ainsi, par exemple, d’améliorer la collaboration au sein d’une équipe exactement comme de la pérennité d’un article de vente.
La méthode PDCA est un outil populaire pour mettre en œuvre un processus d’amélioration continue. Une telle réflexion repose sur le principe qu’une entreprise doit continuer à s’améliorer en permanence pour survivre sur le marché face à la concurrence. La roue de Deming peut servir de plan concret sur la façon de mettre en œuvre l’idée de processus d’amélioration continue.
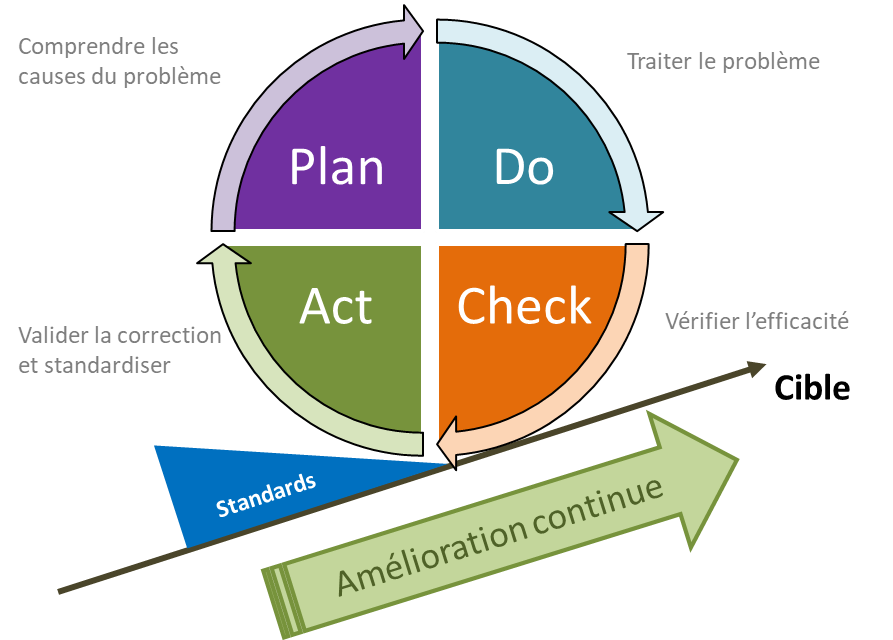
5P
La méthode de base de résolution de problèmes du Lean insiste sur la nécessité de se poser cinq fois la question «pourquoi? » pour aller au-delà des causes symptomatiques et trouver les causes fondamentales (sur lesquelles on pourra alors agir pour éliminer le problème une fois pour toutes). Le piège du «5 pourquoi?» est la déduction en salle. À chaque «pourquoi?» il faut aller sur le terrain (Marche Gemba), et s’adresser à la personne qui fait le travail et qui pourra donner une réponse concrète plutôt qu’une réponse imaginée par déduction.
5M
Le diagramme de causes et effets appelé également diagramme d’Ishikawa, diagramme arêtes de poisson ou 5M (Matière, Matériel, Méthode, Main d’œuvre et Milieu) est un outil développé par Kaoru Ishikawa utilisé dans la gestion de la qualité. Ce diagramme représente de façon graphique les causes aboutissant à un effet. Il peut être utilisé comme outil de modération d’un brainstorming, comme outil de visualisation synthétique et de communication des causes identifiées. Il peut être utilisé dans le cadre de recherche de cause d’un problème existant ou d’identification et gestion des risques lors de la mise en place d’un projet. Ce diagramme se structure habituellement autour des 5M.
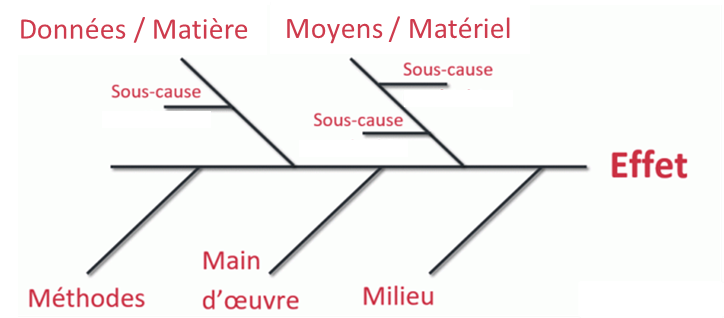
GEMBA WALK
Un gemba walk est un « tour d’usine » ou d’atelier, durant lequel le responsable se rend sur le terrain, « là où cela se passe » (gemba) pour se rendre compte in situ de la situation réelle.
Le gemba walk peut se traduire littéralement par « tour de terrain » ou plus métaphoriquement « marche de la valeur ». Un gemba walk est utile pour :
Apprécier le travail déjà fait, et celui qui reste à faire en matière d’amélioration et d’éradication des dysfonctionnements
Vérifier si le discours lean se retrouve bien dans les pratiques et les faits
Identifier les lieux et opérations créatrices de valeur, et réciproquement les gaspillages
POKA YOKE
Les systèmes anti-erreur ou détrompeurs permettent d’éradiquer les erreurs et ainsi supprimer les contrôles afin de viser un niveau d’excellence qualité (e.g. biseau sur une carte SIM, formes spécifiques des connecteurs informatiques ou audio-visuels) .


AMDEC
L’ AMDEC est l’acronyme de l’Analyse des Modes de Défaillance, de leurs Effets et de leurs Criticités. C’est une méthode qui vise à répertorier pour un processus donné l’ensemble des modes de défaillance qu’on peut lui associer et d’évaluer la criticité de ces défaillances afin de déterminer et de hiérarchiser ses points faibles. Il existe plusieurs types d’AMDEC : l’AMDEC procédé, l’AMDEC produit, l’AMDEC machine, l’AMDEC service et l’AMDEC processus. L’objectif de l’AMDEC est d’évaluer les risques liés à un processus de fabrication. Il pourra s’agir de risques liés à la sécurité, à la qualité, à la performance de production.
Management visuel
Le management visuel contribue à la communication et à l’image de marque de la société.
Son objectif est de définir, à l’aide d’outils visuels, un environnement de travail ayant les qualités suivantes :
Être le plus près possible de l’opérateur
Faciliter la réactivité et donc être une aide à la prise de décision
Faciliter et simplifier la définition des objectifs
Diagramme spaghetti
Le diagramme spaghetti est un outil qui sert à donner une vision claire du flux physique des produits, des dossiers, des individus etc. Il tire son nom de sa ressemblance avec un plat de spaghettis, car lors de son premier tracé, en général, les flux s’entremêlent. Cette visualisation sert à identifier les flux redondants, les croisements récurrents et à mesurer le trajet parcouru par chaque produit ou personne. Il aide à la réimplantation ou réorganisation géographique des machines ou des services pour limiter les déplacements et réduire la non-valeur ajoutée.
Les 5S
La méthode des 5S est une technique de management japonaise visant à l’amélioration continue des tâches effectuées dans les entreprises. Élaborée dans le cadre du système de production de Toyota (en anglais Toyota Production System ou TPS), elle doit son appellation de la première lettre de chacune de cinq opérations constituant autant de principes simples.

La Value Stream Mapping (VSM)
La Value Stream Mapping s’inscrit dans une démarche de mise en œuvre de l’amélioration continue et du Lean. Véritable cartographie visuelle des flux (physiques et d’informations) dans un processus étudié, c’est l’outil de diagnostic par excellence qui permet d’identifier les dysfonctionnements et les axes d’optimisation.
Réussir une VSM, se traduit par :
La réduction des délais de réalisation
La réduction des gaspillages
L’optimisation des ressources
L’amélioration des performances Sécurité/Qualité/Délais/Coûts (SQDC) de l’usine

HOSHIN
La méthode Hoshin est un système de management qui permet à l’entreprise de concentrer tous ses efforts et toutes ses ressources dans la réalisation d’un objectif.
Hoshin est le plus souvent mis en œuvre pour la conduite stratégique de percée pour piloter des actions d'amélioration ou régler des problèmes. Hoshin est un outil à trois fonctions : la communication, la planification et le contrôle. Un des points forts du Hoshin est sa capacité à traduire des objectifs qualitatifs, définis au plus haut niveau, en objectifs quantitatifs et plans d'action. Il permet de focaliser de nombreuses ressources sur un nombre restreint d'actions prioritaires. Cette méthode peut être utilisée dans la gestion de production pour améliorer, d'un point de vue assez large, un des points du triptyque "Coût, Délais, Qualité". Chaque acteur concerné doit élaborer une stratégie pour atteindre l’objectif du niveau supérieur du déploiement.
Single Minute Exchange of Die (SMED)
Le Single Minute Exchange of Die est une méthode de changement rapide de série qui permet de réduire les temps non productifs. Il rend le système de production plus réactif et répond à la demande du client en termes d’optimisation des stocks et des tournées d’approvisionnement.
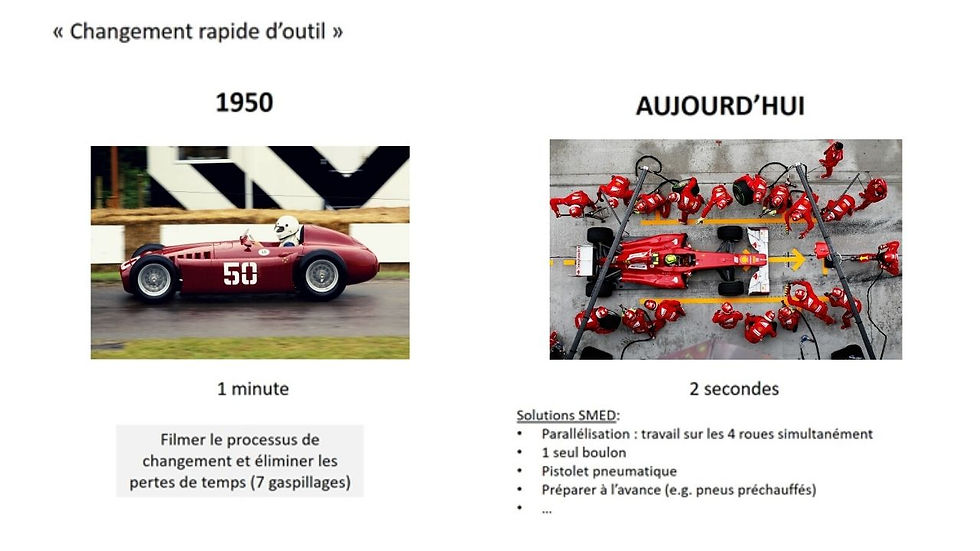
Quels outils pour mon entreprise ?
Déployer une démarche d’amélioration continue demande une certaine connaissance des règles qui assureront l’efficacité d’un Lean Management. De même, la sélection parmi les outils susceptibles de répondre efficacement à telle ou telle problématique nécessite de connaître ces derniers en pratique.
Cost House bénéficie de plus de 15 ans d'expertise dans l’amélioration de la compétitivité des entreprises. Nous vous accompagnons dans la transformation votre activité en mobilisant entre autres le véritable levier de performance qu'est le Lean Management. Nous sélectionnons avec vous les outils les plus adaptés pour amorcer ce nouveau pas vers une performance renforcée.
Pour aller plus loin, découvrez également l'article de SafetyCulture sur le Lean Six Sigma
Pour plus d'informations, contactez-nous
Comentarios